as we inch closer to getting started on our project, we continue to scrutinize our current plans in an effort to create a house that is fine tuned for our needs. as an architect, i want a house that is inspiring and beautiful, and embodies what is important to us. as the owner with a very limited budget, we want to make sure that our cost expectations are realistic. since i’ll be playing general contractor, i want an easy to construct and problem free building.
we’ve taken another pass at redesigning the house with an eye toward efficiency and simplicity – both in terms of square footage and energy. we felt there were a few redundancies, tricky details, and program pieces that we are better off without. here’s a quick snapshot of the progression of the plans.
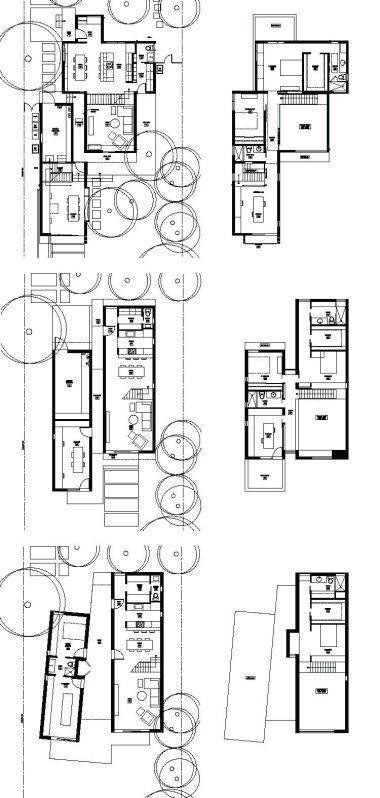
as always, there are a few ideas though that we refuse to give up.
requirement #1: warm, comfortable, and extremely energy efficient
we want to live simply and in a beautiful inspiring place that is warm and comfortable regardless of the time of year. we also want to minimize our footprint and our energy costs. although we will most likely pursue passivhaus certification, the path we take isn’t really as important as the end result. for us, passivhaus is just a means to a better end. our generous friends at brute force collaborative have been providing the expertise to help us get there.
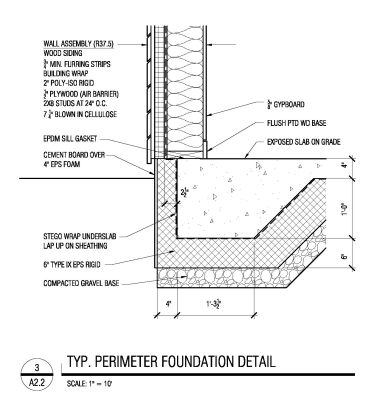
meeting passivhaus requirements means the house will use no more than 4.75 kBTU / ft2 annually for space heating. for the main house, this translates to about 5.27 mBTU or 1544 kWh annually for space heating (we are planning to use electricity to heat the house). at our current rate of around $.09 / kWh, our annual heating bill would be no more than $139.
although we know that the studios will see far less use than the main house, using the same formula yields an annual heating bill for the studios of no more than $51.
requirement #2: wood windows and doors

since we want wood windows and doors, and they need to be extremely high performing to achieve requirement #1, we have been looking at manufacturers based in germany and austria. this is our largest single expense and perhaps an easy target for criticism, as these beauties will need to be shipped overseas. we would love to use a locally produced product, but unfortunately no wood windows made in the US come even close in terms of performance. it’s a bit of a quandary, but brute force collaborative has performed an interesting analysis (based on our previous design) that has us feeling more comfortable with our decision: Can European windows actually save carbon?
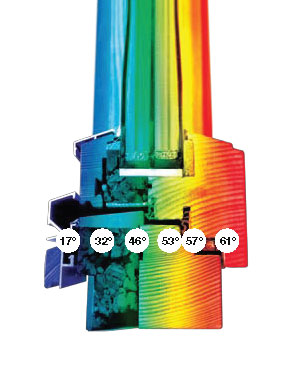
requirement #3: separate work from home
an important part of our program is space to do work and make things. we know we could make a more cost effective and thermally efficient house if we combined our work space with our home, but we like the idea of some separation. we think we can make this simple idea a huge asset.
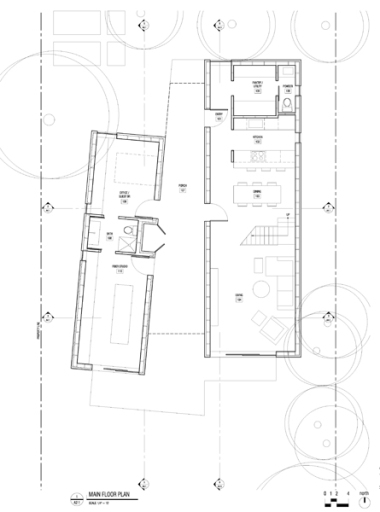
requirement #4: create positive outdoor space
our intention has always been to use the form of the house to shape outdoor space. again, this may contradict requirement #1 but we don’t just want a box sitting in the landscape. we want two boxes sitting in the landscape creating positive space between!
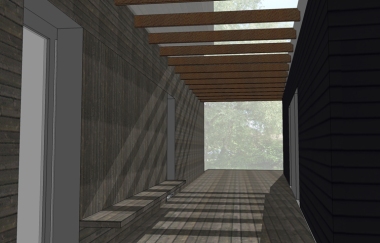
requirement #5: keep it modest and make it beautiful
many people may not agree, but we think these two wood clad boxes with concrete floors, white sheetrock walls, natural wood doors and windows, and flooded with light will be quite beautiful.
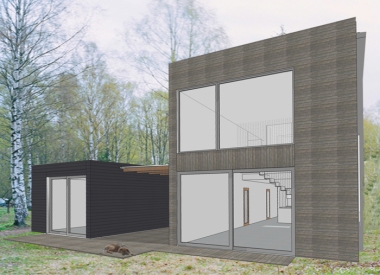